Best practices for achieving operational excellence and efficiency aren’t just buzzwords; they’re the keys to unlocking explosive growth and sustainable success. This deep dive explores how to streamline processes, leverage technology, and cultivate a culture of continuous improvement, ultimately boosting your bottom line and leaving competitors in the dust. We’ll unravel the secrets to optimizing every aspect of your operations, from identifying bottlenecks to implementing cutting-edge automation solutions.
Get ready to transform your business!
From defining operational excellence and its core principles to mastering process optimization and leveraging data analytics, this guide provides a practical roadmap for achieving peak performance. We’ll cover essential KPIs, explore Lean and Six Sigma methodologies, and delve into the crucial role of technology and automation. But it’s not just about tools and techniques; we’ll also examine the importance of employee engagement and building a resilient, future-proof operation.
Prepare for a game-changing journey toward unparalleled efficiency!
Defining Operational Excellence and Efficiency: Best Practices For Achieving Operational Excellence And Efficiency

Operational excellence and efficiency are often used interchangeably, but they represent distinct yet interconnected concepts crucial for business success. While efficiency focuses on maximizing output with minimal input, operational excellence encompasses a broader strategic approach aimed at consistently exceeding customer expectations and achieving sustainable competitive advantage. This involves optimizing all aspects of an organization’s operations, from product development to customer service.
Core Principles of Operational Excellence
Operational excellence is built upon several foundational principles. These principles guide organizations in their pursuit of streamlined processes, reduced waste, and improved overall performance. A key element is a relentless focus on continuous improvement, using methodologies like Lean and Six Sigma to identify and eliminate inefficiencies. Another vital principle is employee empowerment, fostering a culture where every individual is encouraged to contribute to process optimization.
Data-driven decision-making is also critical, utilizing robust analytics to monitor performance, identify areas for improvement, and track progress toward goals. Finally, a customer-centric approach ensures that all operational efforts are aligned with delivering exceptional value to the customer.
Key Performance Indicators (KPIs) for Operational Efficiency, Best practices for achieving operational excellence and efficiency
Measuring operational efficiency requires a carefully selected set of KPIs that provide a holistic view of performance. These KPIs can be categorized into various areas, including productivity, quality, and cost. For instance, productivity can be measured by metrics like units produced per employee or order fulfillment rate. Quality can be assessed through defect rates, customer satisfaction scores, and return rates.
Cost efficiency is often reflected in metrics such as cost per unit, inventory turnover, and operational expenses as a percentage of revenue. Choosing the right KPIs depends on the specific industry, business model, and strategic objectives. For example, a manufacturing company might prioritize production output and defect rates, while a service-based company might focus on customer satisfaction and response times.
Comparison of Operational Excellence Models
Several models provide frameworks for achieving operational excellence. Lean focuses on eliminating waste and maximizing value for the customer, often employing tools like value stream mapping and Kaizen events. Six Sigma emphasizes reducing variation and defects through rigorous statistical analysis and process improvement methodologies like DMAIC (Define, Measure, Analyze, Improve, Control). The Toyota Production System (TPS), a cornerstone of Lean, integrates just-in-time inventory management and continuous improvement principles.
While these models share the common goal of optimizing operations, they differ in their approach and emphasis. Lean prioritizes speed and flexibility, while Six Sigma emphasizes precision and consistency. TPS provides a comprehensive system integrating various Lean principles within a manufacturing context. The optimal model depends on the organization’s specific needs and context.
Relationship Between Operational Excellence and Business Profitability
The impact of operational excellence on business profitability is undeniable. Improved efficiency directly translates to higher margins and increased revenue.
KPI | Measurement Method | Target Value | Improvement Strategies |
Cost per Unit | Actual cost divided by units produced | 10% reduction year-over-year | Process optimization, automation, supplier negotiation |
Order Fulfillment Rate | Number of orders fulfilled on time divided by total orders | 98% | Improved inventory management, streamlined order processing |
Customer Satisfaction Score (CSAT) | Surveys and feedback analysis | 4.5 out of 5 | Enhanced customer service training, improved communication |
Defect Rate | Number of defects divided by total units produced | Less than 1% | Improved quality control processes, employee training |
Process Optimization and Improvement

Operational excellence isn’t just about doing things; it’s about doing them right, efficiently, and consistently. Process optimization and improvement are the cornerstones of achieving this excellence, focusing on streamlining workflows, eliminating waste, and maximizing output. This involves identifying bottlenecks, designing efficient processes, and leveraging technology to automate tasks.
Identifying Bottlenecks and Inefficiencies
Pinpointing bottlenecks and inefficiencies requires a thorough analysis of existing operational processes. This often involves examining workflow diagrams, analyzing data on process times and error rates, and gathering feedback from employees directly involved in the process. Common bottlenecks might include lengthy approval processes, inadequate staffing, outdated technology, or poorly defined roles and responsibilities. For instance, a manufacturing company might find that a specific machine is consistently the slowest part of the production line, creating a bottleneck that impacts overall output.
Identifying these points allows for targeted interventions to improve efficiency. Analyzing data, such as cycle times and defect rates, helps quantify the impact of these bottlenecks and prioritize improvement efforts.
Streamlined Operational Process Flowchart
A well-designed flowchart visually represents the steps in a process, highlighting potential areas for improvement. Consider a simplified order fulfillment process: Customer places order → Order received and processed → Inventory check → Order picked and packed → Shipping label generated → Order shipped → Customer receives order. A streamlined version might incorporate automated inventory checks, integrated shipping label generation, and real-time order tracking, eliminating manual steps and reducing processing time.
The visual representation allows for easy identification of redundancies or unnecessary steps. For example, a flowchart might reveal that a particular step requires multiple approvals, leading to delays. This visual clarity enables effective process redesign.
Lean Methodologies and Their Application
Lean methodologies, originating from the Toyota Production System, focus on eliminating waste (Muda) in all forms. Key Lean principles include Value Stream Mapping (identifying all steps in a process and eliminating non-value-added activities), Kaizen (continuous improvement through small, incremental changes), and 5S (Sort, Set in Order, Shine, Standardize, Sustain – a workplace organization method). For example, a hospital applying Lean principles might use Value Stream Mapping to analyze patient flow, identifying delays in the admission process and implementing changes to streamline it.
Kaizen events could focus on improving the efficiency of medication dispensing, while 5S could be applied to organize the emergency room for improved efficiency and safety.
Implementing Six Sigma Methodologies
Six Sigma aims to reduce process variation and defects by using data-driven methodologies. This involves defining critical-to-quality (CTQ) characteristics, measuring current performance, analyzing the root causes of variation, improving the process, and controlling the improvements to maintain consistency. The DMAIC (Define, Measure, Analyze, Improve, Control) framework is a common approach. A call center implementing Six Sigma might define CTQ characteristics such as call resolution time and customer satisfaction.
By analyzing call data, they can identify the root causes of long resolution times and implement improvements, such as improved training for agents or a more efficient knowledge base. Control charts would then be used to monitor performance and ensure sustained improvements.
Technology for Automation and Optimization
Technology plays a crucial role in automating and optimizing operational processes. Examples include Robotic Process Automation (RPA) for automating repetitive tasks, Enterprise Resource Planning (ERP) systems for integrating various business functions, and Business Process Management (BPM) software for modeling, automating, and optimizing processes. A company using RPA could automate data entry tasks, freeing up employees for more strategic work.
An ERP system can integrate inventory management, order processing, and financial accounting, providing a single source of truth and improving data accuracy. BPM software allows for real-time monitoring of processes, enabling proactive identification and resolution of bottlenecks.
Technology and Automation
In today’s dynamic business environment, leveraging technology and automation is no longer a luxury but a necessity for achieving operational excellence. The integration of smart tools and processes allows companies to streamline workflows, boost productivity, and ultimately, gain a competitive edge. This section explores the transformative power of technology and automation in driving operational efficiency.
Data analytics and automation are key pillars in this transformation. Data analytics provides the insights needed to identify bottlenecks and areas for improvement, while automation streamlines processes, reduces errors, and frees up human capital for more strategic tasks. The synergistic effect of these two components can significantly reduce operational costs and enhance overall efficiency.
Data Analytics for Operational Improvement
Data analytics plays a crucial role in identifying areas ripe for improvement within an organization. By analyzing operational data, businesses can pinpoint inefficiencies, predict potential problems, and make data-driven decisions to optimize processes. For example, analyzing customer service call data can reveal peak call times, common issues, and areas where customer satisfaction is low. This information can then be used to adjust staffing levels, improve training, or redesign processes to improve efficiency and customer satisfaction.
Similarly, analyzing supply chain data can highlight bottlenecks, predict potential disruptions, and optimize inventory management. The insights gleaned from data analytics provide a clear roadmap for targeted improvements.
Best practices for operational excellence hinge on streamlined processes and effective resource allocation. A crucial element of this is mastering remote team management, which significantly impacts productivity. Learn how to achieve this by checking out this insightful guide on how to effectively manage a remote team and boost productivity , and subsequently enhance your overall operational efficiency and achieve excellence.
Automation for Enhanced Efficiency and Cost Reduction
Automation significantly enhances operational efficiency by automating repetitive, time-consuming tasks. This frees up employees to focus on more strategic and value-added activities. For example, automating invoice processing can significantly reduce processing time and errors, leading to faster payments and improved cash flow. Automating data entry tasks eliminates manual errors and frees up administrative staff for more complex tasks.
The reduction in manual labor translates directly into cost savings and improved accuracy. A real-world example is Amazon’s extensive use of robotics in its fulfillment centers, significantly improving order processing speed and reducing labor costs.
Software Solutions Supporting Operational Excellence
Several software solutions are available to support operational excellence initiatives. Choosing the right tools depends on the specific needs and context of the organization. The following list provides a sample of such tools:
Selecting the appropriate software requires a careful assessment of an organization’s specific needs and resources. The solutions listed below represent a diverse range of functionalities and capabilities.
Best practices for achieving operational excellence and efficiency often hinge on a well-defined strategic plan. Successfully navigating the path to operational excellence requires addressing potential roadblocks, and that’s where understanding how to overcome common challenges in strategic business planning comes in; check out this helpful guide on overcoming common challenges in strategic business planning process to ensure your plan is robust.
Ultimately, a strong strategic plan forms the bedrock for streamlined operations and peak efficiency.
- Enterprise Resource Planning (ERP) systems: Such as SAP, Oracle, and Microsoft Dynamics 365, integrate various business functions into a single system, improving data visibility and process coordination.
- Customer Relationship Management (CRM) systems: Like Salesforce and HubSpot, manage customer interactions, automate marketing tasks, and improve customer service efficiency.
- Business Process Management (BPM) suites: Such as Pega and Appian, provide tools for modeling, automating, and monitoring business processes.
- Robotic Process Automation (RPA) tools: Such as UiPath and Automation Anywhere, automate repetitive tasks through software robots.
- Data analytics platforms: Such as Tableau and Power BI, provide tools for data visualization and analysis, enabling data-driven decision-making.
Cloud-Based Solutions for Process Management and Automation
Cloud-based solutions offer scalability, flexibility, and cost-effectiveness for process management and automation. Different cloud providers offer varying levels of functionality and integration capabilities. Some key considerations include security, scalability, and integration with existing systems. For example, a small business might opt for a less expensive, simpler solution, while a large enterprise might require a more robust and scalable platform with advanced security features.
The choice depends on the specific needs and budget of the organization.
Comparison of Process Automation Tools
Tool Name | Key Features | Cost | Integration Capabilities |
---|---|---|---|
UiPath | Robotic Process Automation (RPA), AI-powered automation, attended and unattended automation | Subscription-based, pricing varies based on usage and features | Integrates with various applications and systems via APIs and connectors |
Automation Anywhere | RPA, AI-powered automation, bot store, analytics dashboard | Subscription-based, pricing varies based on usage and features | Integrates with various applications and systems via APIs and connectors |
Zapier | Connects different web applications to automate workflows, no-code automation | Subscription-based, pricing varies based on usage and number of tasks | Integrates with a vast number of applications through pre-built connectors |
People and Culture
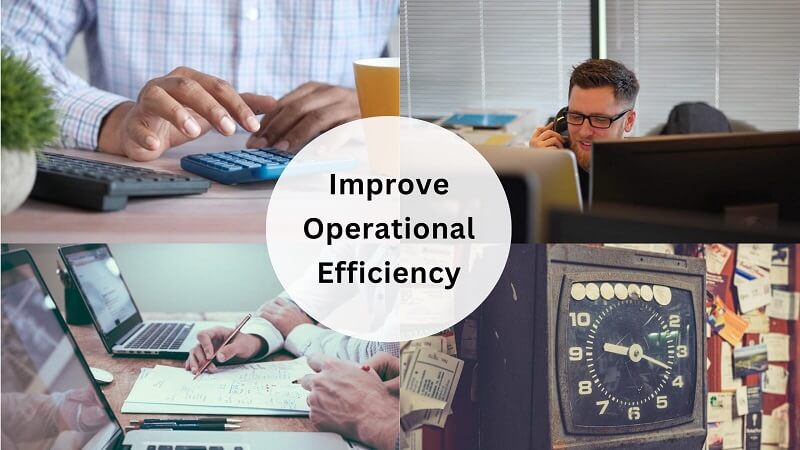
Operational excellence isn’t just about streamlined processes and cutting-edge technology; it’s fundamentally about people. A highly engaged, skilled, and continuously improving workforce is the engine driving true operational excellence. Without a supportive culture and empowered employees, even the most efficient systems will struggle to reach their full potential.Employee engagement is the cornerstone of achieving operational excellence. Engaged employees are more productive, innovative, and committed to quality.
They actively contribute to problem-solving, identify areas for improvement, and take ownership of their work. This translates directly into reduced errors, increased efficiency, and higher customer satisfaction. Conversely, disengaged employees can lead to higher turnover rates, decreased productivity, and a general decline in operational performance.
Employee Engagement and Operational Excellence
Boosting employee engagement requires a multifaceted approach. It starts with creating a work environment that values employee input, fosters open communication, and provides opportunities for growth and development. Regular feedback sessions, recognition programs, and flexible work arrangements can significantly improve employee morale and engagement. Furthermore, providing employees with the resources and autonomy they need to succeed empowers them and increases their sense of ownership, leading to improved performance and a stronger commitment to operational excellence.
For instance, a company that implements a suggestion box system and actively implements employee-suggested improvements demonstrates a commitment to employee engagement and directly improves operational efficiency.
Training and Development for Operational Skills
Effective training and development programs are crucial for upskilling the workforce and ensuring employees possess the necessary skills to excel in their roles. These programs should be tailored to specific operational needs, incorporating both theoretical knowledge and practical application. A blended learning approach, combining online modules, workshops, and on-the-job training, can be highly effective. For example, a manufacturing company could implement a training program focusing on lean manufacturing principles, providing both classroom instruction and hands-on experience in applying these principles to the production line.
Regular skills assessments and performance evaluations help identify areas for improvement and ensure training remains relevant and effective.
Fostering a Culture of Continuous Improvement
A culture of continuous improvement, often referred to as Kaizen, is essential for sustained operational excellence. This involves creating an environment where employees are encouraged to identify and address inefficiencies, suggest improvements, and embrace change. Implementing tools like Six Sigma or Lean methodologies provides a structured framework for continuous improvement initiatives. Regular team meetings dedicated to problem-solving and process optimization are also crucial.
Furthermore, celebrating successes and recognizing contributions reinforces the importance of continuous improvement and motivates employees to participate actively. A company that regularly reviews its processes and incorporates employee feedback into its operational strategies exemplifies a culture of continuous improvement.
Training Program for Improving Operational Efficiency
A comprehensive training program designed to improve operational efficiency could include modules on process mapping, data analysis, problem-solving techniques, and the use of relevant technologies. The program should be delivered through a mix of methods, including online learning, workshops, and mentoring. Participants should be encouraged to apply their learning through practical projects and case studies relevant to their specific roles.
Regular assessments and feedback sessions would ensure that the training is effective and that participants are progressing as expected. For example, a module on lean manufacturing could include a simulation exercise where participants identify and eliminate waste in a simulated production process.
Effective Communication Strategies for Operational Excellence Initiatives
Clear and consistent communication is critical for the successful implementation of operational excellence initiatives. Regular updates, progress reports, and open forums provide employees with the information they need to understand the goals, progress, and impact of these initiatives. Using a variety of communication channels, such as email, intranet postings, and team meetings, ensures that information reaches everyone effectively.
Transparency in communication builds trust and fosters buy-in, encouraging employee participation and commitment. For instance, using visual dashboards to track key performance indicators (KPIs) and sharing progress publicly helps keep employees informed and motivated.
Measuring and Monitoring Performance
Achieving operational excellence isn’t just about implementing new strategies; it’s about knowing if those strategies are actually working. Consistent monitoring and measurement are crucial for identifying areas of strength and weakness, allowing for course correction and continuous improvement. This involves selecting the right metrics, visualizing the data effectively, and analyzing trends to drive informed decision-making.Key Metrics for Tracking ProgressEffective performance monitoring begins with identifying the right key performance indicators (KPIs).
These metrics should directly reflect your operational excellence goals. For example, a manufacturing company might track production output, defect rates, and machine downtime, while a service-based company might focus on customer satisfaction scores, resolution times, and employee productivity. Choosing the right KPIs requires a deep understanding of your business processes and objectives. Irrelevant metrics will only clutter your dashboard and distract from meaningful insights.
Dashboard Visualization of Operational Performance Data
Dashboards are powerful tools for visualizing operational performance data. They present a consolidated view of key metrics, allowing for quick identification of trends and anomalies. Effective dashboards use a combination of charts, graphs, and tables to present data in a clear and concise manner. Color-coding can highlight areas requiring immediate attention, while interactive elements allow for deeper dives into specific data points.
The goal is to make complex data easily understandable for all stakeholders, from frontline employees to senior management.
Analyzing Operational Data to Identify Trends and Patterns
Analyzing operational data goes beyond simply looking at individual metrics. It involves identifying trends and patterns over time to understand the underlying causes of performance variations. Techniques such as regression analysis, time series analysis, and statistical process control (SPC) can be used to identify significant patterns and predict future performance. For example, a retail company might use time series analysis to forecast sales based on historical data and seasonal trends.
By understanding these patterns, businesses can proactively address potential issues and optimize their operations.
Sample Operational Dashboard
Imagine a dashboard displaying four key metrics for a customer service department. The first quadrant shows a line graph illustrating average call resolution time over the past three months, with a clear downward trend indicating improvement. The second quadrant uses a bar chart to compare customer satisfaction scores across different customer segments, highlighting areas where scores are below target. The third quadrant displays a pie chart showing the breakdown of call types, allowing for resource allocation optimization.
Finally, the fourth quadrant uses a real-time counter to show the current number of calls waiting in the queue, providing an immediate snapshot of current workload. Each quadrant uses clear labels, concise titles, and color-coding to emphasize key insights. The dashboard is designed for a quick overview, allowing managers to identify areas needing attention and make informed decisions.
Performance Management Systems for Operational Efficiency
Performance management systems provide a structured framework for tracking and improving operational efficiency. These systems typically involve setting targets, monitoring progress against those targets, providing regular feedback, and implementing corrective actions as needed. Many systems incorporate automated reporting and alerts, ensuring that potential issues are identified promptly. Effective performance management systems promote accountability and encourage continuous improvement by providing clear goals and regular performance reviews.
The use of these systems facilitates data-driven decision-making and helps organizations achieve sustained operational excellence.
Risk Management and Resilience
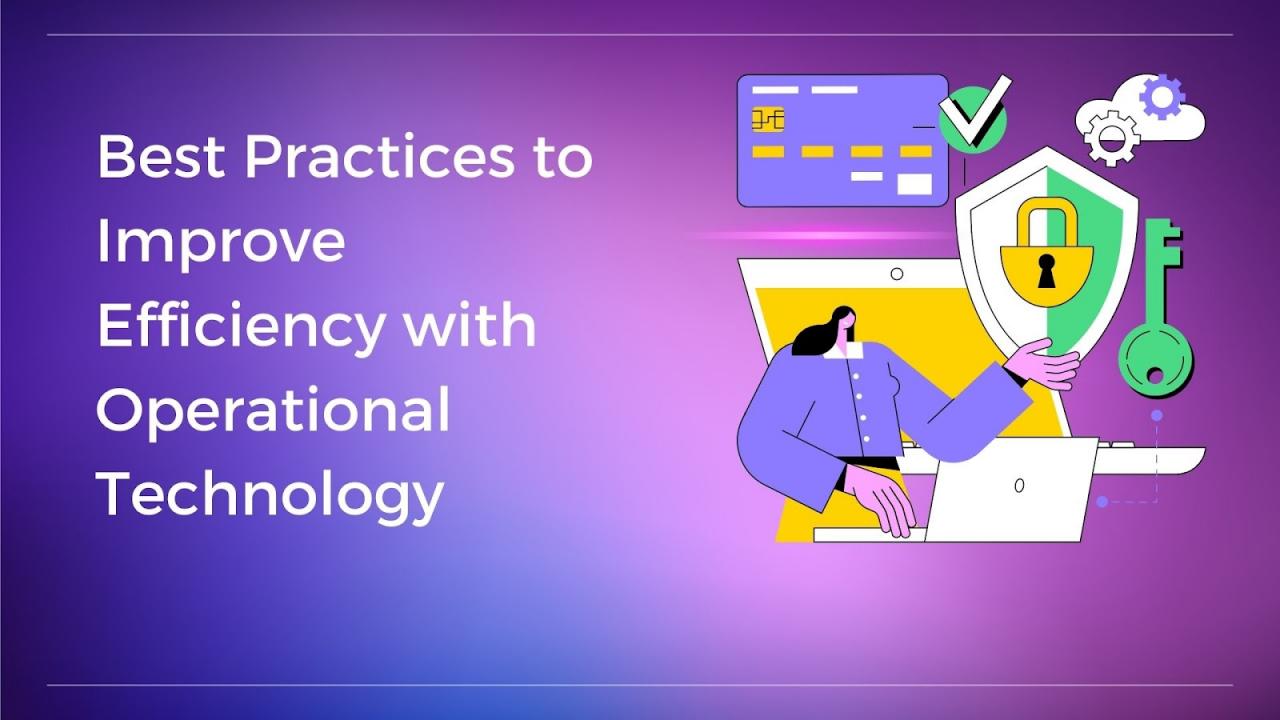
Operational excellence isn’t just about efficiency; it’s about navigating uncertainty and emerging stronger. Building resilience means anticipating potential disruptions and having strategies in place to minimize their impact. A robust risk management framework is crucial for achieving sustained operational excellence. Ignoring potential risks can lead to costly downtime, reputational damage, and even business failure.Proactive risk management involves identifying potential threats, assessing their likelihood and impact, and developing mitigation strategies.
This allows organizations to proactively address vulnerabilities and build a more resilient operational structure. A key component of this is business continuity planning, ensuring operations can continue even during unforeseen circumstances.
Potential Operational Risks and Mitigation Strategies
Several factors can disrupt operational efficiency. These range from internal issues like equipment malfunctions and skill gaps to external factors such as natural disasters and economic downturns. Effective risk management requires a comprehensive understanding of these potential threats.
Business Continuity Planning
Business continuity planning (BCP) is a crucial element of risk management. A well-defined BCP Artikels procedures to ensure critical business functions continue operating during disruptions. This involves identifying critical processes, establishing backup systems, and developing communication protocols. For example, a company might have a backup data center to ensure data accessibility during a power outage, or a detailed communication plan to keep employees informed during a crisis.
Regular testing and updates are essential to ensure the BCP remains relevant and effective.
Risk Assessment Matrix
A risk assessment matrix provides a structured approach to evaluating potential risks. It allows for prioritization of mitigation efforts based on the likelihood and impact of each risk.
Risk | Likelihood | Impact | Mitigation Strategy |
---|---|---|---|
Cybersecurity Breach | Medium | High | Implement robust cybersecurity measures, including firewalls, intrusion detection systems, and employee training. Regular security audits are also crucial. |
Supplier Failure | Low | Medium | Diversify suppliers, establish strong supplier relationships, and include contractual clauses addressing supply chain disruptions. |
Natural Disaster | Low | High | Develop a disaster recovery plan, including backup facilities and data backups. Invest in disaster-resistant infrastructure where feasible. |
Employee Turnover | Medium | Medium | Invest in employee development and retention programs. Implement robust onboarding processes for new hires. |
Economic Downturn | Low | High | Develop financial reserves, diversify revenue streams, and implement cost-cutting measures as needed. Maintain strong relationships with lenders. |
Best Practices for Building Operational Resilience
Building operational resilience requires a multifaceted approach. This includes investing in robust infrastructure, developing flexible processes, fostering a culture of preparedness, and regularly reviewing and updating risk management strategies. For instance, a manufacturing company might implement automated inventory management to minimize stockouts, while a retail company might invest in an e-commerce platform to maintain sales during a physical store closure.
Regular simulations and drills can help test the effectiveness of BCP and identify areas for improvement. Continuous improvement is key to maintaining operational resilience in the face of evolving risks.